Increased productivity
Reduced waiting times for appointments
Freedom for reception to make workshop appointments
Better rotation of courtesy vehicles
Optimising bodywork flows
Bodywork is a specialised operation, with jobs averaging six to seven hours and involving multiple workstations and roles: disassembly/straightening, priming, painting, drying and reassembly. These specialist tasks must be carried out in order by four or five different technicians, with smooth transitions between stages.
As each technician focuses on one specific task, the slightest delay can disrupt the all-important schedule and cause chaos. Flow optimization is necessary.
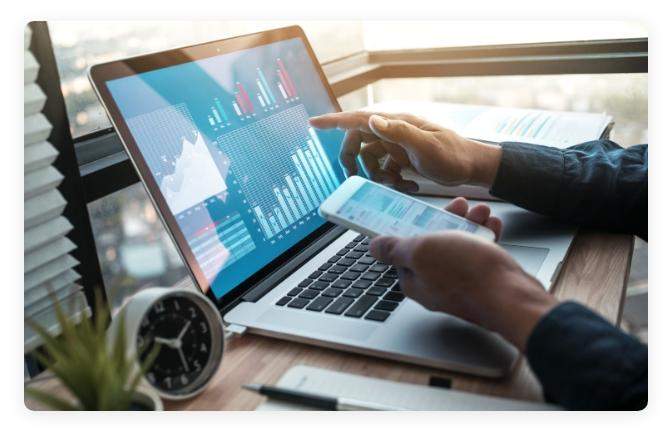
The challenge of digitalising ultra-complex flows
The core of Kairos LS is its allocation engine, a kind of virtual assistant for the workshop manager.
The tool is driven by a set of algorithms that determine the ideal path for optimising lead times, making the team leader’s work much easier – they can visualise the best options available and prioritise operations based on what is needed. With Kairos LS, making the best possible use of resources, optimising customer appointment times and continuously adjusting schedules in response to the workshop’s commitments becomes child’s play. The sheer power of Kairos LS is more than capable of handling the complexity of bodywork projects. The sheer power of Kairos LS is more than capable of handling the complexity of bodywork projects.
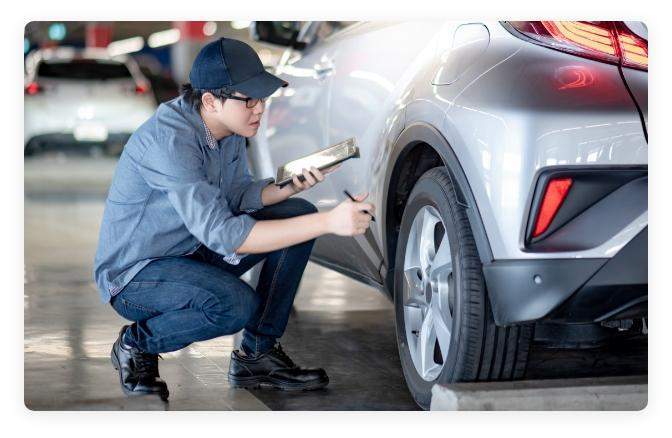
Discover the related features
The Ideal Date
With this module, reception staff can be sure when the vehicle will be returned when they arrange an appointment, making it easier to distribute appointments more evenly across the week.
Allocation engine
The system automatically allocates jobs based on the skills and availability of each technician and each workstation. It can anticipate the impact of delays, prioritising certain projects and adjusting others as a result.
Interface with DMS and inspection software
Precise estimates of times and costs can be generated, with no loss of project management data and no need to enter data more than once into DMS and estimation software.
Discover the related features
The associated features allow you to customise the MecaPlanning solution. You can therefore work with a solution that is entirely adapted to your activity.
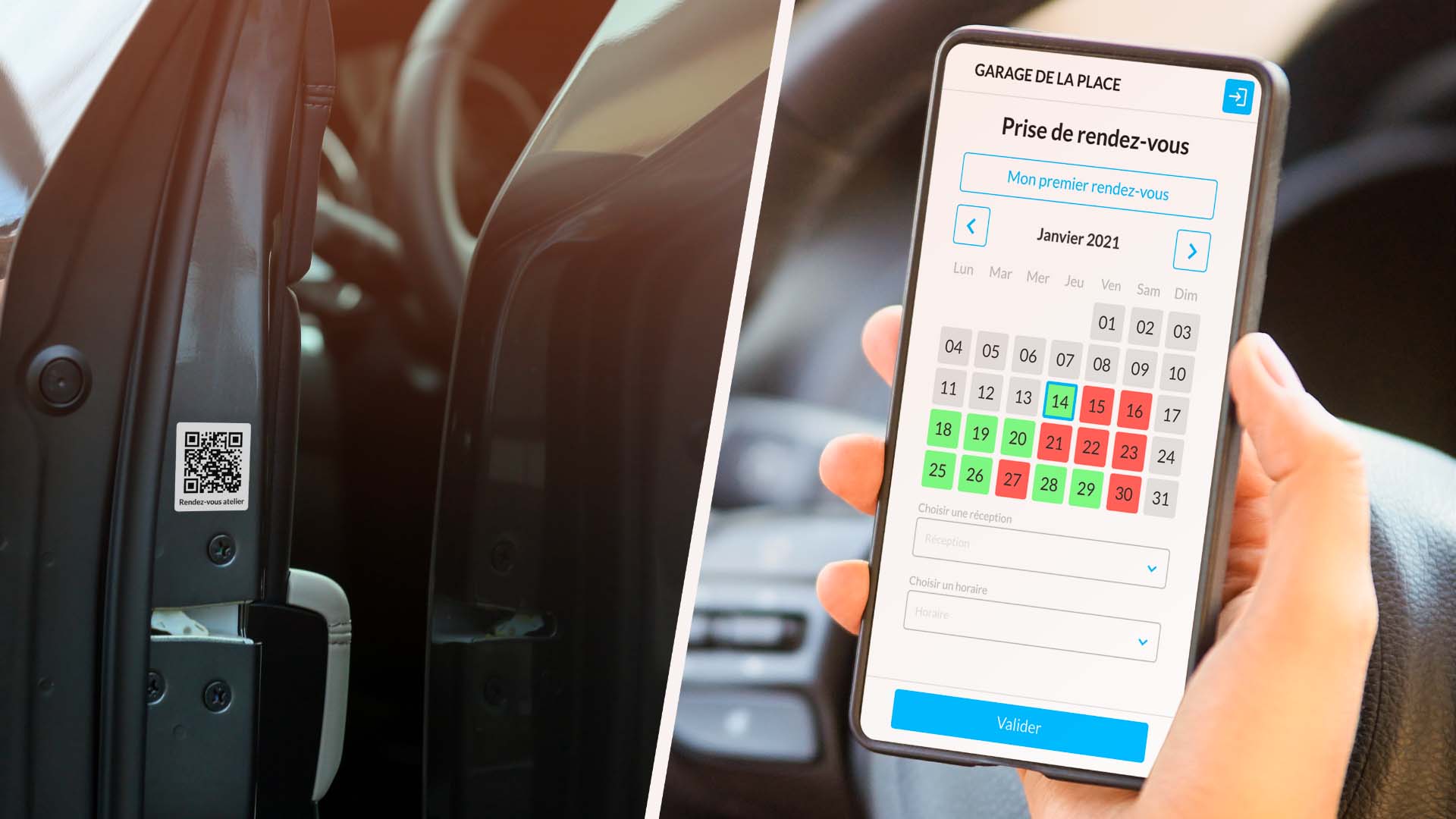
Online appointment booking
3Dsoft was a pioneer in this area, going beyond web forms and callback requests to allow appointments to be made in full via the dealership or manufacturer’s website or via a QR code. This takes place in real time at any time, with no need for human intervention. This smart system takes the workshop’s actual workload into account, predicting accurately how long the operation will take and when the vehicle will be available.
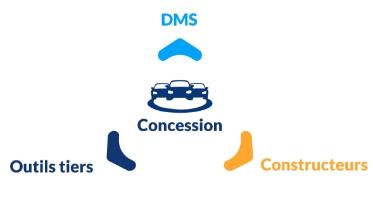
Connectivity with your environment
MecaPlanning can interface with DMS software, manufacturers’ extranets and other partners for a complete, scalable custom ecosystem.
Find out more
Discover our products
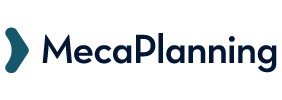
The digital platform for streamlined after-sales management.
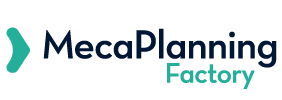
Industrial-scale processes for new and used vehicle preparation centres.
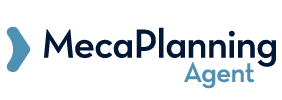
Digital after-sales management for small organisations.
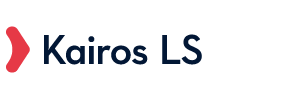
Automate and optimise your bodywork flows.
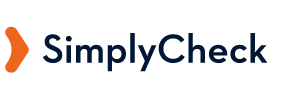
The after-sales reception process revolutionized for more business.